Technologies of the Fusion Fuel Cycle
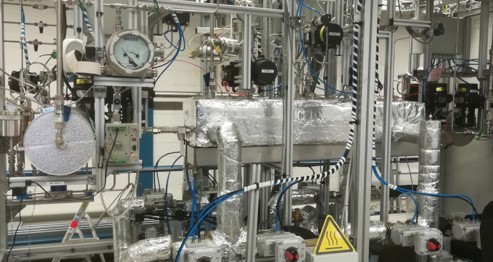
The step from an experimental fusion machine to a 'real' fusion reactor for power generation is considerable, especially from the point of view of the fuel cycle: for reasons of simplicity, fusion machines usually work with protium and deuterium instead of radioactive tritium. For fusion reactors, a closed fuel cycle must be operated with an order of magnitude higher gas throughput for an equimolar mixture of deuterium and tritium, whereby all the special features of tritium handling - such as radiological safety and tritium compatibility of all components used - must be taken into account.
In the case of a fusion reactor, this so-called inner fuel cycle is supplemented by the outer fuel cycle, which contains all systems and components for breeding the tritium required for reactor operation. All systems of the inner and outer fuel cycle must be housed in a specially designed building - the tritium plant - which meets all the necessary safety requirements (such as air and waste water detritiation).
The entire fuel cycle forms a complex process engineering system with a large number of required processes and components that all have to be operated together. The development of such a fuel cycle presents its designers with unprecedented challenges in the areas of process and plant engineering, component development and design as well as safety and modeling. Reliable operation with minimal tritium inventory is only possible if all components of the fuel cycle are coordinated with each other.
In the research field 'Fusion fuel cycle technologies', we are working on the systematic development of such an integrated fuel cycle design in which all components are ideally matched to each other. The starting point for our work is the requirements from plasma physics (e.g. the plasma scenario) and from machine design (e.g. available connection nozzles for the vacuum pumps). Wherever necessary, we develop new processes and components that allow safe and licensable operation of the fuel cycle. For this purpose, we work both with commercially available tools and with codes developed in-house. Our extensive background knowledge in all relevant areas as well as a comprehensive range of software tools and experimental facilities help us to achieve this goal quickly and efficiently.
Our expertise
- Systematic development of an integrated and optimized fuel cycle design, starting from plasma physics requirements
- Identification of development gaps and identification of necessary R&D activities through product development approaches
- Extensive expertise in hydrogen and lithium isotope separation
- Application of process engineering tools for process modeling (e.g. ASPEN®)
- Creation of process engineering flow diagrams
- Analysis of the CAD design of the reactor; development of the design of individual fuel cycle components
Long-term projects
- Development of the fuel cycle for the European DEMO reactor under EUROfusion
- Simulation of tolerable impurities in a fusion plasma and quantification of the necessary gas throughput
- Development of processes for hydrogen and lithium isotope separation (MC-TAS and ICOMAX)
Research infrastructure
- Development platform DIPAK for the complete characterization of a fuel cycle or components of the fuel cycle (up to a scale of 1:1; under construction)
- HESTIA and MAIA facilities for the characterization of active materials for hydrogen isotope separation