Annual report: Highlights 2023
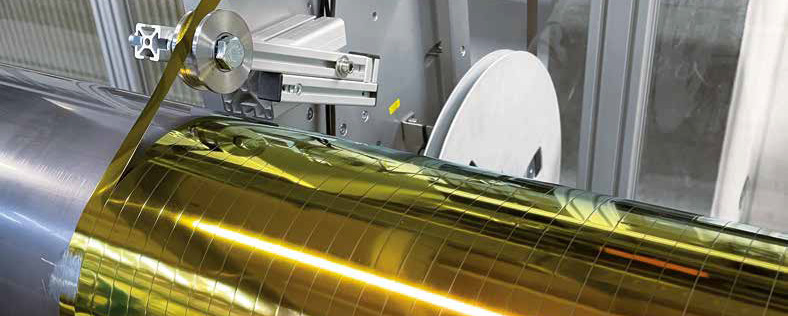
A lot happened at our Institute of Technical Physics in 2023. You can find an overview of the highlights here. You can find the complete report linked below or in the archive.
Superconductor and Cryomaterials
The investigation of new superconductors is an important research focus in the research field of superconductor and cryomaterials.
- In 2023, a comprehensive study on the chemical composition of BaHfO3 nanoparticles in various mixed REBa2 Cu3 O7 phases was completed. Here it was shown that mixing the rare earths (RE) provides an additional increase in pinning force and an improvement in irradiation resistance.
- As part of a long-term cooperation with CERN, the pilot production of high-temperature superconductors from Bruker was set up at KIT and successfully put into operation in 2023. The further aim is to improve the material parameters and produce special strip conductor architectures.
- The joint project AdHyBau (additive hybrid construction methods) was successfully completed in 2023.
- At ITEP, material parameters from 4 to 400 K were essentially determined and, in combination with microstructure investigations, the manufacturing parameters were understood (grain size, defects, porosity). The data is available in a database that can be read directly into design software.
Highlight: Successful commissioning of pilot production of HTS conveyor belt ladders
As part of the KC 4 collaboration project (KIT-CERN Collaboration on Coated Conductor), an HTS pilot production facility was successfully put into operation at ITEP in 2023 and corresponding research work was started. As part of the KC4 project, HTS strip conductor coating systems, which have been developed with great success at an industrial superconductor manufacturer in recent years, have been transferred to KIT.
This will make it possible in future to develop complete HTS strip conductor architectures for special application scenarios at ITEP and produce them in a strip length of up to several hundred meters, so that new coil concepts can be tested, for example. From 2024, this expansion will make it possible for the first time at a research institute in Europe to directly combine current short sample material developments with the HTS tape length requirements of application demonstrators. As part of KC4, special HTS strip conductor architectures that are not available industrially will be developed in the coming years for the development of HTS-based accelerator magnets and their special requirements profile. KC4 will also produce wide HTS strip conductors that are currently not produced industrially and can be used for the development of new coil topologies. KC4 relies on the established combination of ion beam textured metal substrates and their coating using pulsed laser deposition (PLD) and vapor deposition processes for the synthesis of HTS strip conductors. KC4 is an industry-independent project, so that in the medium term it will also be possible to provide interested research institutions and companies with an openly accessible development platform for special HTS strip conductor developments.
The HTS coating process of a coated conductor consists of several individual steps in which, in addition to the actual HTS layer, other buffer and metallic cover layers are applied to a heavily textured metal strip substrate of low thickness (<80 μm) (Figure 9). All relevant coating steps for strip lengths of up to 30 m were successfully put into operation and qualified last year. A special feature of the coating process used in KC4 is that the strip length to be coated is wound onto a cylinder and coated in rotation in an almost always closed oven chamber using PLD. In 1 μm thick HTS coatings, the required project milestones were achieved in 2023 with critical current densities of >300 A/cm at 77 K and an intrinsic field.
Since March 2023, HTS strip conductors have now been routinely synthesized and characterized for further research work as part of the KC4 work. A current focus of the research work is to understand the electromechanical properties of the strip conductors and their relationship with the underlying coating processes.
Superconducting power applications
Coordination: Prof. Dr.-Ing. Mathias Noe
In the research field of energy technology applications, a bridge circuit was realized for the first time using the dynamic resistance of superconductors. The further aim is to further increase the voltage of the circuit and to develop superconducting converters for high-current applications in the future.
- The work at the ITEP on two joint projects to develop a superconducting industrial busbar with a current of 200,000 A and a superconducting magnetic heater could be successfully continued in 2023 so that the final commissioning can be carried out by the industrial partners.
- In the simulation of high-temperature superconductors, it was possible to better understand the current path in the frequently used helical arrangement. This helps to calculate the alternating current losses more accurately.
- In the research topic "Real-time system integration", a Horizon Europe project "Research Facility 2.0" worth 5 million euros was successfully applied for, which will start in 2024. In collaboration with five of the largest accelerators in Europe (ALBA, CERN, DESY, HZB, MAX IV), energy efficiency topics from the component to the system level will be investigated for both physics and energy technology and concrete solutions proposed that will be experimentally validated in demonstration facilities at the accelerator facilities.
Highlight: KIT test field for energy efficiency and grid stability in large research infrastructures - KITTEN
Particle accelerators are energy-intensive systems that offer little flexibility in terms of demand and place high demands on power quality. On the other hand, they strive for better energy efficiency due to high energy costs. The RTSET group, together with the KARA particle accelerator at KIT, has developed the KITTEN research infrastructure to address these challenges in terms of energy efficiency and stability in accelerators.
As a result, a Horizon Europe project "Research Facility 2.0" worth 5 million euros was successfully applied for, which will start in 2024. In collaboration with five of the largest accelerators in Europe (ALBA, CERN, DESY, HZB, MAX IV), energy efficiency topics will be investigated from the component to the system level for both physics and energy technology and concrete solutions will be proposed, which will be experimentally validated in demonstration facilities at the accelerator facilities.
The RTSET group will focus on the digital twinning of accelerators, especially for digital real-time applications, as well as on the optimal placement, design and control of technologies based on power electronics and energy storage.
Superconducting magnet technology
An important task in the research field of superconducting magnet technology is the development of high-temperature superconducting magnets.
- The institute has an apparatus for the robotic winding of non-planar high-temperature superconducting magnets. A new and improved winding hand was realized for this apparatus in 2023, with which further windings will be produced in the coming year.
- An initial conceptual design was created for a hybrid energy pipeline for electricity and liquid hydrogen, which will form the basis for further technical and economic evaluation.
- A rotating machine was designed for the "disk-up-down-assembly" (DUDA) arrangement of high-temperature superconductors patented at KIT and further improved tape stacks were produced. It was also shown how the alternating current losses in this arrangement can be significantly reduced.
- Prof. Dr. Tabea Arndt was awarded the IEEE Prize for continuous and significant contributions to applied superconductivity. This is in recognition of her many years of outstanding technical and scientific achievements.
Highlight: Preparation of an HTS fusion cable section for quench examinations
As part of the EU-CN collaboration agreement in the field of FUSION, ITEP is participating in a measurement campaign to investigate the quench behavior of HTS fusion conductors. Within this program, samples with critical currents of <= 15 kA at 4 K and 11 T will be tested by several research centers in the SULTAN facility of the Paul Scherrer Institute in Villingen, Switzerland. The aim of the test series is to gain a deeper understanding of quench propagation in HTS conductors for fusion applications.
The geometry of the samples is specified by the system: it consists of two straight, approximately 3.6 m long sample legs, which are connected in series via a clamping contact. The current path describes the shape of a "U", which means that both contacts of the sample to the system are at the same end of the sample. Each of the two legs is cooled by a separate helium cooling circuit. This design makes it possible to set individual test temperatures for each sample leg and to induce a targeted quench. This can be triggered either by a heater or by varying the helium temperature.
In 2023, the final steps of specimen production were completed. These included the longitudinal welding to close the two stainless steel half shells of the jacket, the soldering of the connection contacts and the final assembly of the sample legs and the mechanical support to absorb the Lorentz forces of up to 165 kN/m during the experiment.
The two SubSize fusion conductors consist of stranded HTS-CroCo triplets. A temperature measurement system based on fiber Bragg gratings was set up and tested from 3.8 to 400 K in parallel with the sample production. This method enables a high sensor density with low space requirements, Fig. 19: Results of the Ic measurements along the sample. The difference between sample legs #A and #B is due to differences in the layout of the sub-conductors. In contrast to leg #A, the cross-shaped stack of the CroCo conductor in leg #B is additionally twisted. The core consists of a CroCo triplet, with a copper profile soldered to each CroCo for stabilization. The jacket consists of two stainless steel half-shells, enabling temperature measurement directly on the superconductor inside the sample. A cascade of voltage taps and temperature sensors, both inside and on the jacket, should enable the quench propagation to be observed as accurately as possible.
At the end of the year, a functional test at 77 K was successfully carried out after completion of the sample. The critical current and all electrical contacts met expectations or were within the specifications for a successful test campaign in SULTAN. The critical current of the two legs was approximately 4800 A and 4500 A. The expected value was 4800 A without taking into account the magnetic fields of neighboring CroCos. In spring 2024, two more cooling cycles down to 4.2 K are now due to calibrate the glass fiber thermometers and the final leak test before shipping to Switzerland.
Technologies of the fusion fuel cycle
In the research field of fusion fuel cycle technologies, we are developing fundamentally new vacuum technologies and processes for tritium extraction and recovery.
- The simulator developed at ITEP for the fuel cycle of a fusion power plant was used to simulate plasma start-up ramps and show, among other things, that helium peaks at the inlet lead to tritium peaks at the outlet.
- In October, the cryogenic pumps developed at ITEP and manufactured by an industrial partner for the Japanese fusion experiment JT60-SA were delivered.
- The vacuum systems for the divertor test tokamak in Italy were modeled and some design changes were made based on the results.
- Furthermore, the best configuration was found for the metal foil pumps for DEMO. The "Direct Internal Recycling" method developed at the Institute for the DEMO fuel cycle is now also being set up on a large scale.
- To this end, the plans for the "Direct Internal Recycling Development Platform Karlsruhe" (DIPAK) have been revised and initial construction planning has begun. This plant replicates two of the three circuits of the fuel cycle and includes all new technologies such as pellet injection, metal foil pumps, mercury pumps and temperature swing absorption for isotope separation.
Highlight: Divertor cryogenic pumps for JT-60SA delivered
In a project lasting several years, the divertor pump system for the JT-60SA fusion machine in Japan was designed, constructed and finally built and successfully accepted together with Fusion for Energy and industrial partners at the Institute of Vacuum Technology. With a plasma volume of around 130 m³, JT-60SA (Figure 10) is the largest superconducting tokamak after ITER and pursues the ultimate goal of finally clarifying the open questions regarding the long-pulse operation of a tokamak.
The large-scale facility is located in Naka, Japan, on the site of the former JT60U test facility. It is currently in its first operating phase. In 2024, the machine will be retrofitted with additional technical systems. This includes a powerful divertor pump system, which the Vacuum division is responsible for providing together with the fusion agency 'Fusion for Energy'.
The pump project can be divided into three different phases.
- Concept development phase (2012-2017). The JT-60SA project was initiated in 2007 as part of the "Broader Approach" agreement between the EU and Japan. The vacuum sector has been involved in the development of the scientific program and the definition of the technologies required for this since 2012. As part of this work, the requirements for the divertor pump system were defined. Deviating from the original plan to use cryocondensation pumps, the decision was made in 2017 in favor of a cryosorption system with activated carbon-coated 4-K pump surfaces. This required extensive calculations to predict the operating window of the pumps and to derive an initial cost estimate to check the plausibility of the effort required for construction.
- Design phase (2017-2020). In several development stages with corresponding design reviews, a 3D CAD file with all individual parts (Figure 11) and a set of 2D production drawings were finally developed. Based on this design, 'Fusion for Energy' carried out a tender and finally commissioned the German manufacturer Research Instruments.
- Manufacturing phase (2021-2023). A total of ten identical cryopumps were manufactured, together with a 'practice' cryopump to validate the manufacturing steps and their testing procedures. Figure 12 shows the central elements of the cryopump. At the heart of this are the cryopanels, two of which are installed in each 'pump blade'. They are coated with activated carbon so that helium can be pumped well at the intended operating temperature of 3.8 K. There is a closed thermal shield on the back of the panel at 80 K. In the course of production, a number of individual manufacturing steps had to be redeveloped. Nevertheless, the time had come on October 3, 2023: all cryogenic pumps had been delivered to Japan and had successfully passed the incoming inspection.
The commissioning of JT-60SA is currently underway, and the first plasma was generated on October 23, 2023. The JT-60SA research plan covers the plant's lifetime of approximately 20 years. The use of divertor vacuum systems to control the plasma will play a central role in this.